Today, aluminum has rapidly developed into an indispensable material in the lives of every Chinese. Aluminum alloy doors and windows, aluminum alloy furniture, bathroom appliances, cooking utensils, household appliances in Chinese homes, all means of transportation used for travel, such as bicycles, electric vehicles, motorcycles, cars, high-speed trains, airplanes, ships, computers and mobile phones used in daily work and life, etc., all use aluminum to varying degrees, and the application of aluminum is constantly expanding.
It is precisely because of the huge demand for aluminum among 1.38 billion Chinese that my country’s aluminum industry has leaped to the top of the world in just over 20 years (the rapid development of my country’s aluminum industry began in 1991). At present, China’s demand for bauxite, production and consumption of alumina, production and consumption of electrolytic aluminum, and production and consumption of aluminum materials have all leapt to the top in the world, and have exceeded the total production and consumption of all developed countries. At the same time, it has also created world alumina and electrolytic aluminum production giants such as Weiqiao, and created world aluminum alloy rod production giants such as Innovation. Reform and opening up have provided broad space for the development of my country’s aluminum industry.
The technology and equipment achievements accumulated by foreign aluminum companies that have worked hard in the aluminum industry for more than 120 years have given wings to the development of China’s aluminum industry, which has enabled China’s aluminum industry to complete the journey that foreign aluminum industries have taken more than 120 years to complete in just over 20 years.
1.Discovery and utilization of bauxite
Bauxite is the best raw material for producing aluminum, accounting for more than 90% of the world’s total bauxite production. Bauxite was first discovered by French geologists in 1821. To produce aluminum from bauxite, alumina must first be produced, and then aluminum is produced by electrolysis. Bauxite mining began in France in 1873, and the production of alumina from bauxite began in 1894, using the Bayer process. By 1900, there was a small amount of bauxite mining in countries such as France, Italy and the United States, with an annual output of only 90,000 tons.
With the development of modern industry, aluminum as a metal and alloy has been applied to aviation and military industries, and then expanded to civilian industries. Since then, the aluminum industry has developed rapidly. By 2016, the world’s electrolytic aluminum production has reached more than 57 million tons, and the mined bauxite in 2016 increased to 262 million tons. According to the data of the U.S. Bureau of Mines in 2017, the world’s bauxite reserves are 28 billion tons. The bauxite resources given by the earth to mankind provide raw materials for the world and China’s aluminum industry.
2.Bayer process for producing alumina
The Bayer process is a widely used industrial method for producing alumina from bauxite. It was invented by Austrian engineer Bayer in 1887. Currently, 95% of the world’s alumina companies use the Bayer process to produce alumina.
3.Hall-Heroult process for producing electrolytic aluminum
In 1886, American Hall and Frenchman Heroux independently invented the cryolite-alumina molten salt electrolysis method to produce aluminum. So far, all the aluminum in the world is produced by electrolysis.
4.Aluminum alloy melting
Melting is a method of alloying metals. It is a process that changes the physical state of metals by heating, so that the base metal and alloying components are melted into a uniform melt according to the required ratio, and meet the internal purity, casting temperature and other specific requirements. The quality of the melt has a decisive influence on the processing performance and final use performance of aluminum materials. If the quality of the melt is inherently insufficient, it will bring potential dangers to the use of the product. Therefore, melting is a key process that plays a dominant role in the quality of processed products.
5.Aluminum melt processing technology
Inclusions and hydrogen content in metals have significant adverse effects on the strength, fatigue resistance, corrosion resistance, stress corrosion cracking performance and processing performance of materials. Effectively controlling the hydrogen content and oxidized inclusion content of the melt to improve the quality of cast bars and rolled plates has become a common goal pursued by metallurgy, casting and materials industries in various countries. At present, electromagnetic stirring, refining in the furnace, online deterioration outside the furnace, online degassing and online filtration methods are widely used to reduce the hydrogen content and inclusion content in the aluminum alloy melt and improve the mechanical properties and appearance quality of the ingot.
6.Direct water-cooled ingot
Aluminum Corporation of America invented the technology of direct water-cooled casting, which was adopted by all Aluminum plants in the 1930s. In the 1950s, ingots cast by direct water-cooled casting could be used to manufacture large products required by the aerospace, shipbuilding and transportation industries. With the advancement of direct water-cooled casting technology and equipment, the size of ingots has been continuously increased. Currently, slabs can weigh up to 45 tons and the diameter of aluminum bars for extrusion can reach 1.2 meters.
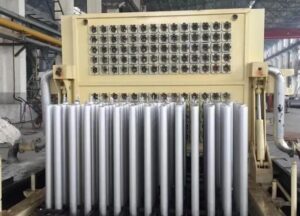
7.Aluminum machining and die casting
Aluminum processing is to process aluminum billets into materials by plastic processing methods. The main methods include rolling, extrusion, stretching and forging. Among aluminum and aluminum alloy processed materials, rolled materials (plates, strips, bars, foils) and extruded materials (tubes, bars, profiles, wires) are the most widely used and have the largest output. According to statistics, the annual output of these two types of materials accounts for about 58% and 39% of the world’s total annual output of aluminum (on average), respectively. The rest of the aluminum processed materials, such as forged products, only account for a few percent of the total aluminum output.
Pressure casting, also known as die casting, is a casting method that pours molten alloy liquid into a pressure chamber, fills the cavity of a steel mold at high speed, and solidifies the alloy liquid under pressure to form a casting. Die casting machines, die casting alloys and die casting molds are the three major elements of die casting production, and none of them can be missing. The so-called die casting process is to organically combine these three major elements to produce qualified castings with good appearance and internal quality and dimensions that meet the requirements of drawings or agreements in a stable, rhythmic and efficient manner.
8.Heat treatable aluminum alloy
In 1908, German scientists discovered the aging strengthening phenomenon of aluminum-copper-magnesium alloys, which greatly improved the strength of aluminum alloys and expanded the application areas of aluminum alloys.
New alloys are constantly being developed by various countries. At present, there are 680 deformed aluminum alloys registered by the Aluminum Association of America. Among them, the most used is the 6063 aluminum alloy in the aluminum-magnesium-silicon system registered by the American Aluminum Company in 1954.
9.Aluminum surface treatment technology
In the past sixty years, the surface treatment technology of aluminum products has developed rapidly. After surface treatment, aluminum alloy products give people a very beautiful and exquisite appearance. Chemical conversion film treatment is one of our most common surface treatment technologies. Anodizing, composite anodizing, micro-arc oxidation, electrophoretic painting, etc. are all chemical conversion film treatments. Chemical conversion film treatment is more mature and stable than other surface treatment technologies. But now more composite technology is used. Composite technology is to combine the advantages of various technologies and avoid their disadvantages. Such as arc glow technology, ion beam combined sputtering technology, etc., ion beam combined sputtering technology combines magnetron sputtering with ion implantation, ion sputtering has the advantages of fast speed, low temperature, good bonding strength, etc. There is also a combination of laser and sputtering.
10.Environmental protection technology in the aluminum industry
The main pollutants in the aluminum industry include red mud produced during the production of alumina, fluorine-containing waste gas from electrolysis, flue gas from carbon calcination and roasting, waste from electrolytic cell overhaul, waste water and waste oil from aluminum processing, and other industrial wastes. These waste slag, waste gas, and waste water have always been the focus of environmental monitoring, and are related to occupational health and safety and social, ecological, and economic sustainable development.
In order to enable the aluminum industry to continue to develop in the direction of green and low carbonization, corresponding environmental protection and energy-saving equipment has been continuously developed, striving to improve the overall environmental protection level of the aluminum industry from various aspects such as environmental protection, intelligence, and integrated control.
While enjoying the technological and equipment achievements of the world’s aluminum industry, every aluminum-related company at home and abroad has also made contributions of varying sizes to the development of the aluminum industry.
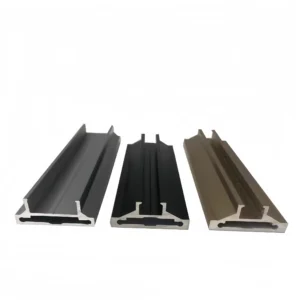